ਨਿਵੇਸ਼ ਕਾਸਟਿੰਗ ਮੋਮ ਦੇ ਉੱਲੀ ਦੀ ਸਤਹ 'ਤੇ ਰਿਫ੍ਰੈਕਟਰੀ ਕੋਟਿੰਗ ਦੀਆਂ ਕਈ ਪਰਤਾਂ ਨੂੰ ਕੋਟ ਕਰਨਾ ਹੈ। ਇਸ ਨੂੰ ਕਠੋਰ ਅਤੇ ਸੁੱਕਣ ਤੋਂ ਬਾਅਦ, ਮੋਮ ਦੇ ਉੱਲੀ ਦੀ ਸ਼ਕਲ ਨਾਲ ਮੇਲ ਖਾਂਦਾ ਇੱਕ ਖੋਲ ਪ੍ਰਾਪਤ ਕਰਨ ਲਈ ਮੋਮ ਦੇ ਉੱਲੀ ਨੂੰ ਗਰਮ ਕਰਕੇ ਪਿਘਲਾ ਦਿੱਤਾ ਜਾਂਦਾ ਹੈ। ਪਕਾਉਣ ਤੋਂ ਬਾਅਦ, ਇਸਨੂੰ ਕਾਸਟਿੰਗ ਪ੍ਰਾਪਤ ਕਰਨ ਦੇ ਇੱਕ ਢੰਗ ਵਿੱਚ ਡੋਲ੍ਹਿਆ ਜਾਂਦਾ ਹੈ, ਇਸਲਈ ਇਸਨੂੰ ਗੁਆਚਿਆ ਮੋਮ ਕਾਸਟਿੰਗ ਵੀ ਕਿਹਾ ਜਾਂਦਾ ਹੈ। ਉਤਪਾਦਨ ਤਕਨਾਲੋਜੀ ਦੇ ਨਿਰੰਤਰ ਸੁਧਾਰ ਦੇ ਨਾਲ, ਨਵੀਂ ਮੋਮ ਮੋਲਡਿੰਗ ਪ੍ਰਕਿਰਿਆਵਾਂ ਪ੍ਰਗਟ ਹੁੰਦੀਆਂ ਰਹਿੰਦੀਆਂ ਹਨ, ਅਤੇ ਮੋਲਡਿੰਗ ਲਈ ਉਪਲਬਧ ਸਮੱਗਰੀ ਦੀ ਵਿਭਿੰਨਤਾ ਵਧ ਰਹੀ ਹੈ. ਹੁਣ ਉੱਲੀ ਨੂੰ ਹਟਾਉਣ ਦਾ ਤਰੀਕਾ ਹੁਣ ਪਿਘਲਣ ਤੱਕ ਸੀਮਿਤ ਨਹੀਂ ਹੈ, ਅਤੇ ਮੋਲਡਿੰਗ ਸਮੱਗਰੀ ਮੋਮ ਸਮੱਗਰੀ ਤੱਕ ਸੀਮਿਤ ਨਹੀਂ ਹੈ. ਪਲਾਸਟਿਕ ਦੇ ਮੋਲਡ ਵੀ ਵਰਤੇ ਜਾ ਸਕਦੇ ਹਨ। ਕਿਉਂਕਿ ਇਸ ਵਿਧੀ ਦੁਆਰਾ ਪ੍ਰਾਪਤ ਕੀਤੀਆਂ ਕਾਸਟਿੰਗਾਂ ਵਿੱਚ ਉੱਚ ਆਯਾਮੀ ਸ਼ੁੱਧਤਾ ਅਤੇ ਹੇਠਲੇ ਸਤਹ ਦੇ ਖੁਰਦਰੇ ਮੁੱਲ ਹੁੰਦੇ ਹਨ, ਇਸ ਨੂੰ ਸ਼ੁੱਧਤਾ ਕਾਸਟਿੰਗ ਵੀ ਕਿਹਾ ਜਾਂਦਾ ਹੈ।
ਦੀ ਬੁਨਿਆਦੀ ਵਿਸ਼ੇਸ਼ਤਾਨਿਵੇਸ਼ ਕਾਸਟਿੰਗਇਹ ਹੈ ਕਿ ਸ਼ੈੱਲ ਬਣਾਉਣ ਵੇਲੇ ਇੱਕ ਪਿਘਲਣਯੋਗ ਡਿਸਪੋਸੇਬਲ ਮੋਲਡ ਵਰਤਿਆ ਜਾਂਦਾ ਹੈ। ਕਿਉਂਕਿ ਉੱਲੀ ਨੂੰ ਖਿੱਚਣ ਦੀ ਕੋਈ ਲੋੜ ਨਹੀਂ ਹੈ, ਸ਼ੈੱਲ ਇੱਕ ਵਿਭਾਜਨ ਸਤਹ ਤੋਂ ਬਿਨਾਂ ਅਟੁੱਟ ਹੈ, ਅਤੇ ਸ਼ੈੱਲ ਸ਼ਾਨਦਾਰ ਉੱਚ ਤਾਪਮਾਨ ਪ੍ਰਦਰਸ਼ਨ ਦੇ ਨਾਲ ਰਿਫ੍ਰੈਕਟਰੀ ਸਮੱਗਰੀ ਦਾ ਬਣਿਆ ਹੁੰਦਾ ਹੈ। ਨਿਵੇਸ਼ ਕਾਸਟਿੰਗ ਗੁੰਝਲਦਾਰ-ਆਕਾਰ ਦੀਆਂ ਕਾਸਟਿੰਗਾਂ ਪੈਦਾ ਕਰ ਸਕਦੀ ਹੈ, ਜਿਸ ਦੀ ਘੱਟੋ-ਘੱਟ ਕੰਧ ਮੋਟਾਈ 0.3mm ਅਤੇ ਕਾਸਟਿੰਗ ਮੋਰੀ ਦਾ ਘੱਟੋ-ਘੱਟ ਵਿਆਸ 0.5mm ਹੋਵੇ। ਕਈ ਵਾਰ ਉਤਪਾਦਨ ਵਿੱਚ, ਕਈ ਹਿੱਸਿਆਂ ਦੇ ਬਣੇ ਕੁਝ ਹਿੱਸਿਆਂ ਨੂੰ ਬਣਤਰ ਨੂੰ ਬਦਲ ਕੇ ਅਤੇ ਨਿਵੇਸ਼ ਕਾਸਟਿੰਗ ਦੁਆਰਾ ਸਿੱਧੇ ਰੂਪ ਵਿੱਚ ਬਣਾਇਆ ਜਾ ਸਕਦਾ ਹੈ। ਇਹ ਪ੍ਰੋਸੈਸਿੰਗ ਮੈਨ-ਘੰਟੇ ਅਤੇ ਧਾਤ ਸਮੱਗਰੀ ਦੀ ਖਪਤ ਨੂੰ ਬਚਾ ਸਕਦਾ ਹੈ, ਅਤੇ ਬਣਤਰ ਬਣਾ ਸਕਦਾ ਹੈਕਾਸਟਿੰਗ ਹਿੱਸੇਹੋਰ ਵਾਜਬ.
ਨਿਵੇਸ਼ ਕਾਸਟਿੰਗ ਦੁਆਰਾ ਪੈਦਾ ਕੀਤੀ ਕਾਸਟਿੰਗ ਦਾ ਭਾਰ ਆਮ ਤੌਰ 'ਤੇ ਦਸਾਂ ਗ੍ਰਾਮ ਤੋਂ ਕਈ ਕਿਲੋਗ੍ਰਾਮ, ਜਾਂ ਇੱਥੋਂ ਤੱਕ ਕਿ ਦਸਾਂ ਕਿਲੋਗ੍ਰਾਮ ਤੱਕ ਹੁੰਦਾ ਹੈ। ਮੋਲਡਿੰਗ ਸਮੱਗਰੀ ਦੀ ਕਾਰਗੁਜ਼ਾਰੀ ਦੀ ਸੀਮਾ ਅਤੇ ਸ਼ੈੱਲ ਬਣਾਉਣ ਵਿੱਚ ਮੁਸ਼ਕਲ ਦੇ ਕਾਰਨ ਬਹੁਤ ਜ਼ਿਆਦਾ ਭਾਰੀ ਕਾਸਟਿੰਗ ਨਿਵੇਸ਼ ਕਾਸਟਿੰਗ ਲਈ ਢੁਕਵੇਂ ਨਹੀਂ ਹਨ।
ਨਿਵੇਸ਼ ਕਾਸਟਿੰਗ ਦੁਆਰਾ ਨਿਰਮਿਤ ਕਾਸਟਿੰਗਮਿਸ਼ਰਤ ਮਿਸ਼ਰਣਾਂ ਦੀਆਂ ਕਿਸਮਾਂ ਦੁਆਰਾ ਸੀਮਿਤ ਨਹੀਂ ਹਨ, ਖਾਸ ਤੌਰ 'ਤੇ ਉਨ੍ਹਾਂ ਮਿਸ਼ਰਣਾਂ ਲਈ ਜਿਨ੍ਹਾਂ ਨੂੰ ਕੱਟਣਾ ਜਾਂ ਬਣਾਉਣਾ ਮੁਸ਼ਕਲ ਹੈ, ਜੋ ਇਸਦੀ ਉੱਤਮਤਾ ਨੂੰ ਦਰਸਾ ਸਕਦੇ ਹਨ। ਹਾਲਾਂਕਿ, ਨਿਵੇਸ਼ ਕਾਸਟਿੰਗ ਉਤਪਾਦਨ ਵਿੱਚ ਵੀ ਕੁਝ ਕਮੀਆਂ ਹਨ, ਮੁੱਖ ਤੌਰ 'ਤੇ ਵੱਡੀ ਗਿਣਤੀ ਵਿੱਚ ਪ੍ਰਕਿਰਿਆਵਾਂ, ਲੰਬੇ ਉਤਪਾਦਨ ਚੱਕਰ, ਗੁੰਝਲਦਾਰ ਤਕਨੀਕੀ ਪ੍ਰਕਿਰਿਆਵਾਂ, ਅਤੇ ਕਾਸਟਿੰਗ ਦੀ ਗੁਣਵੱਤਾ ਨੂੰ ਪ੍ਰਭਾਵਿਤ ਕਰਨ ਵਾਲੇ ਬਹੁਤ ਸਾਰੇ ਕਾਰਕ, ਜਿਨ੍ਹਾਂ ਨੂੰ ਉਤਪਾਦਨ ਨੂੰ ਸਥਿਰ ਕਰਨ ਲਈ ਸਖਤੀ ਨਾਲ ਨਿਯੰਤਰਿਤ ਕੀਤਾ ਜਾਣਾ ਚਾਹੀਦਾ ਹੈ।
ਹੋਰ ਕਾਸਟਿੰਗ ਵਿਧੀਆਂ ਦੇ ਮੁਕਾਬਲੇ, ਨਿਵੇਸ਼ ਕਾਸਟਿੰਗ ਦੀ ਕਮਾਲ ਦੀ ਵਿਸ਼ੇਸ਼ਤਾ ਸ਼ੈੱਲ ਬਣਾਉਣ ਲਈ ਪਿਘਲਣਯੋਗ ਮੋਲਡਾਂ ਦੀ ਵਰਤੋਂ ਹੈ। ਹਰ ਵਾਰ ਜਦੋਂ ਇੱਕ ਸ਼ੈੱਲ ਬਣਾਇਆ ਜਾਂਦਾ ਹੈ ਤਾਂ ਇੱਕ ਨਿਵੇਸ਼ ਮੋਲਡ ਦੀ ਖਪਤ ਹੁੰਦੀ ਹੈ। ਉੱਚ ਆਯਾਮੀ ਸ਼ੁੱਧਤਾ ਅਤੇ ਘੱਟ ਸਤਹ ਦੇ ਖੁਰਦਰੇਪਣ ਮੁੱਲਾਂ ਦੇ ਨਾਲ ਉੱਚ-ਗੁਣਵੱਤਾ ਵਾਲੀ ਕਾਸਟਿੰਗ ਪ੍ਰਾਪਤ ਕਰਨ ਲਈ ਜ਼ਰੂਰੀ ਸ਼ਰਤ ਉੱਚ ਆਯਾਮੀ ਸ਼ੁੱਧਤਾ ਅਤੇ ਘੱਟ ਸਤਹ ਖੁਰਦਰੀ ਮੁੱਲਾਂ ਵਾਲਾ ਇੱਕ ਨਿਵੇਸ਼ ਮੋਲਡ ਹੈ। ਇਸ ਲਈ, ਮੋਲਡਿੰਗ ਸਮੱਗਰੀ ਦੀ ਕਾਰਗੁਜ਼ਾਰੀ (ਮੋਲਡ ਸਮੱਗਰੀ ਵਜੋਂ ਜਾਣੀ ਜਾਂਦੀ ਹੈ), ਮੋਲਡਿੰਗ ਦੀ ਗੁਣਵੱਤਾ (ਨਿਵੇਸ਼ ਨੂੰ ਦਬਾਉਣ ਲਈ ਵਰਤਿਆ ਜਾਣ ਵਾਲਾ ਪੈਟਰਨ) ਅਤੇ ਮੋਲਡਿੰਗ ਪ੍ਰਕਿਰਿਆ ਸਿੱਧੇ ਤੌਰ 'ਤੇ ਨਿਵੇਸ਼ ਕਾਸਟਿੰਗ ਦੀ ਗੁਣਵੱਤਾ ਨੂੰ ਪ੍ਰਭਾਵਤ ਕਰੇਗੀ।
ਨਿਵੇਸ਼ ਕਾਸਟਿੰਗ ਮੋਲਡ ਵਰਤਮਾਨ ਵਿੱਚ ਆਮ ਤੌਰ 'ਤੇ ਮਲਟੀਲੇਅਰ ਰਿਫ੍ਰੈਕਟਰੀ ਸਮੱਗਰੀ ਦੇ ਬਣੇ ਸ਼ੈੱਲ ਵਿੱਚ ਵਰਤੇ ਜਾਂਦੇ ਹਨ। ਮੋਡੀਊਲ ਨੂੰ ਡੁਬੋਏ ਜਾਣ ਅਤੇ ਰਿਫ੍ਰੈਕਟਰੀ ਕੋਟਿੰਗ ਨਾਲ ਲੇਪ ਕੀਤੇ ਜਾਣ ਤੋਂ ਬਾਅਦ, ਦਾਣੇਦਾਰ ਰਿਫ੍ਰੈਕਟਰੀ ਸਮੱਗਰੀ ਨੂੰ ਛਿੜਕ ਦਿਓ, ਅਤੇ ਫਿਰ ਸੁੱਕਾ ਅਤੇ ਸਖ਼ਤ ਕਰੋ, ਅਤੇ ਇਸ ਪ੍ਰਕਿਰਿਆ ਨੂੰ ਕਈ ਵਾਰ ਦੁਹਰਾਓ ਜਦੋਂ ਤੱਕ ਰਿਫ੍ਰੈਕਟਰੀ ਸਮੱਗਰੀ ਦੀ ਪਰਤ ਲੋੜੀਂਦੀ ਮੋਟਾਈ ਤੱਕ ਨਹੀਂ ਪਹੁੰਚ ਜਾਂਦੀ। ਇਸ ਤਰ੍ਹਾਂ, ਮੋਡੀਊਲ ਉੱਤੇ ਇੱਕ ਮਲਟੀ-ਲੇਅਰ ਸ਼ੈੱਲ ਬਣਦਾ ਹੈ, ਜੋ ਆਮ ਤੌਰ 'ਤੇ ਪੂਰੀ ਤਰ੍ਹਾਂ ਸੁੱਕਣ ਅਤੇ ਸਖ਼ਤ ਹੋਣ ਲਈ ਸਮੇਂ ਦੀ ਇੱਕ ਮਿਆਦ ਲਈ ਖੜ੍ਹਾ ਹੁੰਦਾ ਹੈ, ਅਤੇ ਫਿਰ ਮਲਟੀ-ਲੇਅਰ ਸ਼ੈੱਲ ਪ੍ਰਾਪਤ ਕਰਨ ਲਈ ਢਾਹਿਆ ਜਾਂਦਾ ਹੈ। ਕੁਝ ਮਲਟੀ-ਲੇਅਰ ਸ਼ੈੱਲਾਂ ਨੂੰ ਰੇਤ ਨਾਲ ਭਰਨ ਦੀ ਲੋੜ ਹੁੰਦੀ ਹੈ, ਅਤੇ ਕੁਝ ਨਹੀਂ ਕਰਦੇ। ਭੁੰਨਣ ਤੋਂ ਬਾਅਦ, ਉਹਨਾਂ ਨੂੰ ਸਿੱਧਾ ਡੋਲ੍ਹਿਆ ਜਾ ਸਕਦਾ ਹੈ, ਜਿਸ ਨੂੰ ਉੱਚ-ਸ਼ਕਤੀ ਵਾਲਾ ਸ਼ੈੱਲ ਕਿਹਾ ਜਾਂਦਾ ਹੈ।
ਸ਼ੈੱਲ ਦੀ ਗੁਣਵੱਤਾ ਦਾ ਸਿੱਧਾ ਸਬੰਧ ਕਾਸਟਿੰਗ ਦੀ ਗੁਣਵੱਤਾ ਨਾਲ ਹੁੰਦਾ ਹੈ। ਸ਼ੈੱਲ ਦੀਆਂ ਕੰਮ ਕਰਨ ਦੀਆਂ ਸਥਿਤੀਆਂ ਦੇ ਅਨੁਸਾਰ, ਸ਼ੈੱਲ ਦੀ ਕਾਰਗੁਜ਼ਾਰੀ ਦੀਆਂ ਜ਼ਰੂਰਤਾਂ ਵਿੱਚ ਮੁੱਖ ਤੌਰ 'ਤੇ ਸ਼ਾਮਲ ਹਨ:
1) ਇਸ ਵਿੱਚ ਉੱਚ ਸਾਧਾਰਨ ਤਾਪਮਾਨ ਦੀ ਤਾਕਤ, ਉੱਚਿਤ ਉੱਚ ਤਾਪਮਾਨ ਦੀ ਤਾਕਤ ਅਤੇ ਘੱਟ ਬਚੀ ਤਾਕਤ ਹੈ।
2) ਇਸ ਵਿੱਚ ਚੰਗੀ ਹਵਾ ਦੀ ਪਾਰਦਰਸ਼ਤਾ (ਖਾਸ ਕਰਕੇ ਉੱਚ ਤਾਪਮਾਨ ਵਾਲੀ ਹਵਾ ਪਾਰਦਰਸ਼ੀਤਾ) ਅਤੇ ਥਰਮਲ ਚਾਲਕਤਾ ਹੈ।
3) ਰੇਖਿਕ ਪਸਾਰ ਗੁਣਾਂਕ ਛੋਟਾ ਹੈ, ਥਰਮਲ ਵਿਸਥਾਰ ਘੱਟ ਹੈ ਅਤੇ ਵਿਸਥਾਰ ਇਕਸਾਰ ਹੈ।
4) ਤੇਜ਼ ਠੰਡੇ ਅਤੇ ਗਰਮੀ ਅਤੇ ਥਰਮੋਕੈਮੀਕਲ ਸਥਿਰਤਾ ਲਈ ਸ਼ਾਨਦਾਰ ਵਿਰੋਧ.
ਸ਼ੈੱਲ ਦੀਆਂ ਇਹ ਵਿਸ਼ੇਸ਼ਤਾਵਾਂ ਸ਼ੈੱਲ ਬਣਾਉਣ ਅਤੇ ਸ਼ੈੱਲ ਬਣਾਉਣ ਦੀ ਪ੍ਰਕਿਰਿਆ ਵਿੱਚ ਵਰਤੀਆਂ ਜਾਣ ਵਾਲੀਆਂ ਸਮੱਗਰੀਆਂ ਨਾਲ ਨੇੜਿਓਂ ਸਬੰਧਤ ਹਨ। ਸ਼ੈੱਲ ਸਮੱਗਰੀਆਂ ਵਿੱਚ ਰਿਫ੍ਰੈਕਟਰੀ ਸਮੱਗਰੀ, ਬਾਈਂਡਰ, ਘੋਲਨ ਵਾਲੇ, ਹਾਰਡਨਰ, ਸਰਫੈਕਟੈਂਟਸ, ਆਦਿ ਸ਼ਾਮਲ ਹਨ। ਇਹਨਾਂ ਵਿੱਚੋਂ, ਰਿਫ੍ਰੈਕਟਰੀ ਸਮੱਗਰੀ ਅਤੇ ਬਾਈਂਡਰ ਸਿੱਧੇ ਸ਼ੈੱਲ ਬਣਾਉਂਦੇ ਹਨ, ਜੋ ਕਿ ਮੁੱਖ ਸ਼ੈੱਲ ਸਮੱਗਰੀ ਹੈ। ਨਿਵੇਸ਼ ਕਾਸਟਿੰਗ ਵਿੱਚ ਵਰਤੀਆਂ ਜਾਣ ਵਾਲੀਆਂ ਰੀਫ੍ਰੈਕਟਰੀ ਸਮੱਗਰੀ ਮੁੱਖ ਤੌਰ 'ਤੇ ਸਿਲਿਕਾ ਰੇਤ, ਕੋਰੰਡਮ ਅਤੇ ਐਲੂਮਿਨੋਸਿਲੀਕੇਟ ਰਿਫ੍ਰੈਕਟਰੀਜ਼ (ਜਿਵੇਂ ਕਿ ਰਿਫ੍ਰੈਕਟਰੀ ਮਿੱਟੀ ਅਤੇ ਐਲੂਮੀਨੀਅਮ ਬੈਨੇਡੀਅਮ, ਆਦਿ) ਹਨ। ਇਸ ਤੋਂ ਇਲਾਵਾ, ਜ਼ੀਰਕੋਨ ਰੇਤ ਅਤੇ ਮੈਗਨੀਸ਼ੀਆ ਰੇਤ ਨੂੰ ਕਈ ਵਾਰ ਵਰਤਿਆ ਜਾਂਦਾ ਹੈ।
ਪਾਊਡਰਡ ਰਿਫ੍ਰੈਕਟਰੀ ਸਮੱਗਰੀ ਅਤੇ ਬਾਈਂਡਰ ਰਿਫ੍ਰੈਕਟਰੀ ਕੋਟਿੰਗ ਵਿੱਚ ਤਿਆਰ ਕੀਤੇ ਜਾਂਦੇ ਹਨ, ਅਤੇ ਸ਼ੈੱਲ ਬਣਾਏ ਜਾਣ 'ਤੇ ਰਿਫ੍ਰੈਕਟਰੀ ਕੋਟਿੰਗ 'ਤੇ ਦਾਣੇਦਾਰ ਰਿਫ੍ਰੈਕਟਰੀ ਸਮੱਗਰੀ ਨੂੰ ਛਿੜਕਿਆ ਜਾਂਦਾ ਹੈ। ਰਿਫ੍ਰੈਕਟਰੀ ਕੋਟਿੰਗਾਂ ਵਿੱਚ ਵਰਤੇ ਜਾਂਦੇ ਬਾਈਂਡਰਾਂ ਵਿੱਚ ਮੁੱਖ ਤੌਰ 'ਤੇ ਐਥਾਈਲ ਸਿਲੀਕੇਟ ਹਾਈਡ੍ਰੋਲਾਈਸੇਟ, ਪਾਣੀ ਦਾ ਗਲਾਸ ਅਤੇ ਸਿਲਿਕਾ ਸੋਲ ਸ਼ਾਮਲ ਹੁੰਦੇ ਹਨ। ਈਥਾਈਲ ਸਿਲੀਕੇਟ ਨਾਲ ਤਿਆਰ ਕੀਤੇ ਪੇਂਟ ਵਿੱਚ ਚੰਗੀ ਕੋਟਿੰਗ ਵਿਸ਼ੇਸ਼ਤਾਵਾਂ, ਉੱਚ ਸ਼ੈੱਲ ਤਾਕਤ, ਛੋਟੀ ਥਰਮਲ ਵਿਕਾਰ, ਪ੍ਰਾਪਤ ਕਾਸਟਿੰਗ ਦੀ ਉੱਚ ਆਯਾਮੀ ਸ਼ੁੱਧਤਾ, ਅਤੇ ਚੰਗੀ ਸਤਹ ਗੁਣਵੱਤਾ ਹੁੰਦੀ ਹੈ। ਇਹ ਜਿਆਦਾਤਰ ਮਹੱਤਵਪੂਰਨ ਮਿਸ਼ਰਤ ਸਟੀਲ ਕਾਸਟਿੰਗ ਅਤੇ ਉੱਚ ਸਤਹ ਗੁਣਵੱਤਾ ਲੋੜਾਂ ਦੇ ਨਾਲ ਹੋਰ ਕਾਸਟਿੰਗ ਪੈਦਾ ਕਰਨ ਲਈ ਵਰਤਿਆ ਜਾਂਦਾ ਹੈ. ਚੀਨ ਵਿੱਚ ਪੈਦਾ ਹੋਣ ਵਾਲੀ ਇਥਾਈਲ ਸਿਲੀਕੇਟ ਦੀ SiO2 ਸਮੱਗਰੀ ਆਮ ਤੌਰ 'ਤੇ 30% ਤੋਂ 34% (ਪੁੰਜ ਦਾ ਅੰਸ਼) ਹੁੰਦੀ ਹੈ, ਇਸਲਈ ਇਸਨੂੰ ਈਥਾਈਲ ਸਿਲੀਕੇਟ 32 ਕਿਹਾ ਜਾਂਦਾ ਹੈ (32 ਈਥਾਈਲ ਸਿਲੀਕੇਟ ਵਿੱਚ SiO2 ਦੇ ਔਸਤ ਪੁੰਜ ਅੰਸ਼ ਨੂੰ ਦਰਸਾਉਂਦਾ ਹੈ)। ਈਥਾਈਲ ਸਿਲੀਕੇਟ ਹਾਈਡ੍ਰੌਲਿਸਿਸ ਤੋਂ ਬਾਅਦ ਹੀ ਇੱਕ ਬਾਈਡਿੰਗ ਭੂਮਿਕਾ ਨਿਭਾ ਸਕਦਾ ਹੈ।
ਪਾਣੀ ਦੇ ਗਲਾਸ ਨਾਲ ਤਿਆਰ ਕੋਟਿੰਗ ਸ਼ੈੱਲ ਨੂੰ ਵਿਗਾੜਨਾ ਅਤੇ ਚੀਰਨਾ ਆਸਾਨ ਹੈ। ਈਥਾਈਲ ਸਿਲੀਕੇਟ ਦੀ ਤੁਲਨਾ ਵਿੱਚ, ਪੈਦਾ ਕੀਤੀਆਂ ਕਾਸਟਿੰਗਾਂ ਵਿੱਚ ਘੱਟ ਆਯਾਮੀ ਸ਼ੁੱਧਤਾ ਅਤੇ ਉੱਚ ਸਤਹ ਖੁਰਦਰੀ ਹੁੰਦੀ ਹੈ। ਵਾਟਰ ਗਲਾਸ ਬਾਈਂਡਰ ਛੋਟੇ ਆਮ ਸਟੀਲ ਕਾਸਟਿੰਗ ਦੇ ਉਤਪਾਦਨ ਲਈ ਢੁਕਵਾਂ ਹੈ ਅਤੇਗੈਰ-ਫੈਰਸ ਮਿਸ਼ਰਤ ਕਾਸਟਿੰਗ. ਨਿਵੇਸ਼ ਕਾਸਟਿੰਗ ਲਈ ਪਾਣੀ ਦੇ ਗਲਾਸ ਵਿੱਚ ਆਮ ਤੌਰ 'ਤੇ 3.0~3.4 ਦਾ ਮਾਡਿਊਲਸ ਅਤੇ 1.27~1.34 g/cm3 ਦੀ ਘਣਤਾ ਹੁੰਦੀ ਹੈ।
ਸਿਲਿਕਾ ਸੋਲ ਬਾਈਂਡਰ ਸਿਲਿਕਿਕ ਐਸਿਡ ਦਾ ਇੱਕ ਜਲਮਈ ਘੋਲ ਹੈ, ਜਿਸਨੂੰ ਸਿਲਿਕਾ ਸੋਲ ਵੀ ਕਿਹਾ ਜਾਂਦਾ ਹੈ। ਇਸਦੀ ਕੀਮਤ ਐਥਾਈਲ ਸਿਲੀਕੇਟ ਨਾਲੋਂ 1/3~1/2 ਘੱਟ ਹੈ। ਸਿਲਿਕਾ ਸੋਲ ਨੂੰ ਬਾਈਂਡਰ ਵਜੋਂ ਵਰਤ ਕੇ ਪੈਦਾ ਕੀਤੀ ਕਾਸਟਿੰਗ ਦੀ ਗੁਣਵੱਤਾ ਪਾਣੀ ਦੇ ਗਲਾਸ ਨਾਲੋਂ ਉੱਚੀ ਹੈ। ਬਾਈਡਿੰਗ ਏਜੰਟ ਨੂੰ ਬਹੁਤ ਸੁਧਾਰਿਆ ਗਿਆ ਹੈ. ਸਿਲਿਕਾ ਸੋਲ ਵਿੱਚ ਚੰਗੀ ਸਥਿਰਤਾ ਹੈ ਅਤੇ ਇਸਨੂੰ ਲੰਬੇ ਸਮੇਂ ਲਈ ਸਟੋਰ ਕੀਤਾ ਜਾ ਸਕਦਾ ਹੈ। ਸ਼ੈੱਲ ਬਣਾਉਣ ਵੇਲੇ ਇਸ ਨੂੰ ਵਿਸ਼ੇਸ਼ ਹਾਰਡਨਰਾਂ ਦੀ ਲੋੜ ਨਹੀਂ ਹੁੰਦੀ। ਸ਼ੈੱਲ ਦੀ ਉੱਚ ਤਾਪਮਾਨ ਦੀ ਤਾਕਤ ਐਥਾਈਲ ਸਿਲੀਕੇਟ ਸ਼ੈੱਲਾਂ ਨਾਲੋਂ ਬਿਹਤਰ ਹੈ, ਪਰ ਸਿਲਿਕਾ ਸੋਲ ਨਿਵੇਸ਼ ਲਈ ਕਮਜ਼ੋਰ ਗਿੱਲਾ ਹੈ ਅਤੇ ਸਖ਼ਤ ਹੋਣ ਵਿੱਚ ਜ਼ਿਆਦਾ ਸਮਾਂ ਲੈਂਦਾ ਹੈ। ਸ਼ੈੱਲ ਬਣਾਉਣ ਦੀਆਂ ਮੁੱਖ ਪ੍ਰਕਿਰਿਆਵਾਂ ਵਿੱਚ ਮੋਡਿਊਲ ਡੀਗਰੇਸਿੰਗ, ਕੋਟਿੰਗ ਅਤੇ ਸੈਂਡਿੰਗ, ਸੁਕਾਉਣਾ ਅਤੇ ਸਖ਼ਤ ਕਰਨਾ, ਡਿਮੋਲਡਿੰਗ ਅਤੇ ਭੁੰਨਣਾ ਸ਼ਾਮਲ ਹਨ।
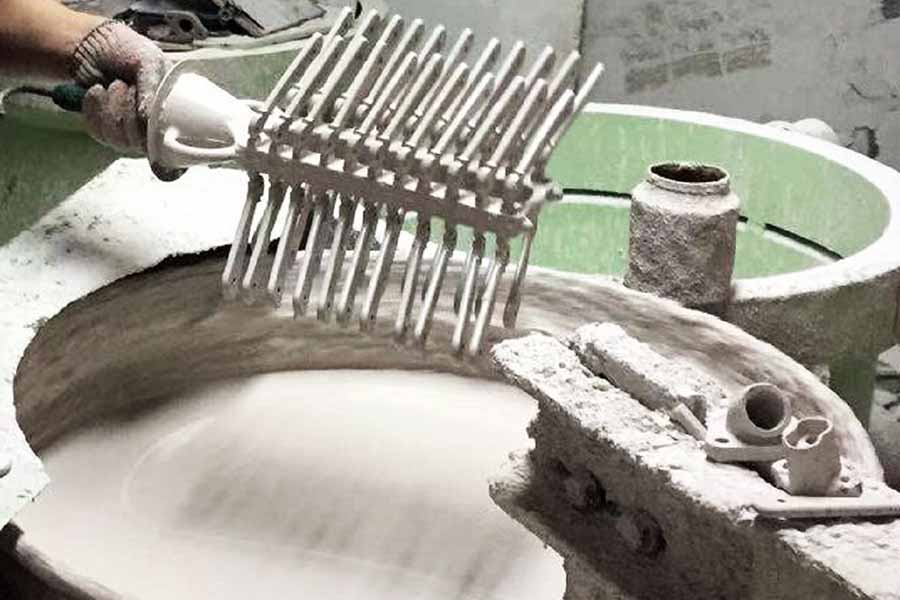
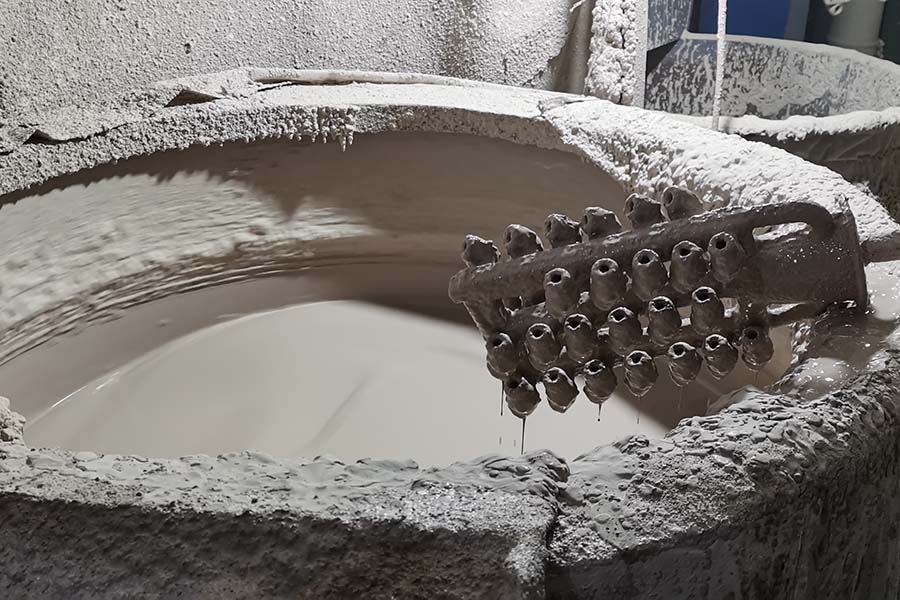
ਪੋਸਟ ਟਾਈਮ: ਫਰਵਰੀ-11-2021